There are a number of ways to “play with” this technique, transfer lace on these machines becomes a hand technique aided by needle selection made by the card reader, based on punched holes mylar markings.
Method 1: single carriage using published cards that are for lace carriages that transfer only (Brother, Knitking, Toyota, Studio/Knitmaster fashion lace started on the appropriate row ).
1. Lock card on the first row as would be done on a standard machine.
2. KH carriage starts out on the Left side with end needle selection canceled.
3. Remove yarn from the feeder, store on left. Deactivate the row counter (flip automatic tripper back ).
4. First selection row is made left to right. Transfers can then be made by hand in direction of arrows, moving stitches on the selected needles to their left, away from the carriage. All needles must be returned to the B position.
5. Push in both part (slip) buttons.
One thing to keep in mind: when the KH carriage is set to slip, it is the selected needles that actually knit stitches. If the carriage moves across those same needles with no yarn in the feeder, selected needles will drop their corresponding stitches.
6. Set card to advance “normally”, move the carriage to the left.
7. Continue to make transfers that the lace carriage would have made in the direction as marked on the card until knit row markings are reached and no needles are selected.
8. Release part buttons, leave KC engaged.
9. Put yarn back in the feeder and the row count tripper back into work or advance RC by hand for the required number of knit rows
10. Knit 2 rows or if lace pattern requires 4 or more rows of knitting between repeats KC needs to be turned off for 2 rows less than needed, then turned back on for the last 2 knit rows. A lot to keep track of, but still quicker than hand knitting. Forgetting to put yarn in the feeder for knit rows or to set carriage back to slip for transfer selection rows will result in what I have come to fondly refer to as drop-itis.
Method 2: using 2 carriages, extension rails.
Bulky extension rails are shaped differently than those for the standard KM, their front “arm” quite a bit longer than the rear one. Rails are handy when knitting very wide pieces, a necessity when multiple carriages are in use, and especially when both are set to KC and engage the belt.
This method’s movements mimic those of traditional lace knitting in the standard Brother machine.
1. The “lace” carriage on left is set to slip in both directions, its RC tripper is in the off position.
2. The KH carriage on the right set to knit, its row count tripper on.
3. End needle selection is canceled on both carriages.
4. Left carriage operates “like” the lace carriage in terms of needle selection, but it is the knitter who hand manipulates the transfers, which are made in the same direction as the marked arrows on the card, away from the carriage.
5. When no needles are selected and the black arrow markings for knit rows on the lace card is reached, the “Lace” carriage is returned to its position off the bed on the left
6. The R, KH carriage then knits required rows, returns to rest on the R rail, and the process begins over again.
Since the KH carriage is not on KC and the card does not advance on knit rows, no adjustments need to be made to its settings if multiple knit rows are required.
Method 3: using studio simple lace cards (those cards that are not “suitable” for brother KMs). These cards are intended for machines that select and knit with each carriage pass
1. Using Studio card with A-side up lock card on row 3.
2. Knit carriage: KC in use, cancel end needle selection, no cam buttons throughout (this results in needle selection, but fabric created is in stocking stitch).
3. Row counter on 3
4. Make the first selection row right to left. Transfer stitches selected onto adjacent needles toward the same side as carriage (in this instance from right to left). All needles must be returned to the B position.
5. Release card, set card to advance normally. After each selection row, hand transfers continue to be made toward the carriage.
I found it easier to track the direction of transfers by remembering to move toward the carriage than to follow the direction of arrow markings on the card which do match, with even-numbered rows transferred toward the right, odd-numbered ones toward left.
The simple lace cards may also be used on the standard punchcard brother KM. Two carriages are selecting needles, so usual precautions for such knitting must be used, with each carriage off the bed and on the extension rail while the alternate carriage moves toward it from the opposite side. As the carriages are switched, operating from the opposite side, the previous selection is repeated.
1. Studio punchcard is locked on Row 3, KC (knit carriage) on right. The main carriage is set to KC, end needle selection is canceled, no cam buttons are used, it will knit with every pass it makes and selects the needles for the subsequent transfer row.
2. Release card, knit one row from right to left
3. KCOL, the Lace Carriage is engaged on the opposite Right side and moves toward the knit carriage to make the transfers. As it travels across the bed it will reselect the same needles (now empty). After transfers are completed, make a second pass with the lace carriage, and remove it from the needle bed.
5. The KH carriage is now free to make its pass for the single row of knitting to the opposite side, from Left to Right.
6. The lace carriage is engaged opposite to the knit carriage (now the left) and makes transfers toward it once again. It makes a second pass to its original place on right and is removed from the bed to be used again from the left. The process is repeated for the pattern. The Studio simple lace card may of course be redrawn with extra rows needed for standard use on the Brother KM.
the punchcard
the resulting transfers on both the bulky and standard Brother machines
Extension rails for the bulky machine are available for purchase, are handy when producing wider pieces and particularly if knitting on the whole bed. Be aware if purchasing them, that the rails for the 9 mm machine are a different size, noticeable in the photo below. The bulky rail has a white tag on it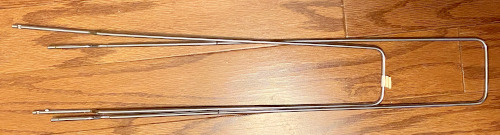